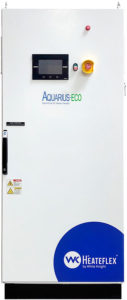
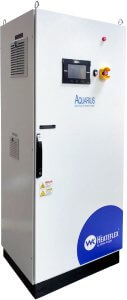
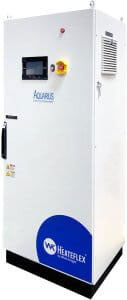
Ultrapure Water Conservation with Aquarius-ECO™
Heated Ultrapure Water (UPW) is critical in Semiconductor manufacturing to ensure purity and high yields. With constant demand for chips, and increasing needs to conserve water, the world’s largest OEMs and Fabs have been upgrading their tools and facilities to focus on enhancing water and energy efficiencies.
The Aquarius® DI Recirculating Heating System was initially released in 2006 to meet certain customer requests to go Green. This provided our customers with a method of eliminating the trickle flow.
This product was ahead of its time and proved to be an invaluable system for most of our leading-edge customers. With proven results and engineering aptitude, WK evaluated ways to improve the performance and provide an upgraded system to better conserve water and energy, while still providing the same temperature performance our customers are acclimated to.
Our Aquarius-ECO™ is an upgraded recirculating Aquarius® DI water heating system that utilizes a White Knight PSA060 pump with Heateflex’s advanced heating technology. This provides customers with:
- Reduce water
- Reduce energy consumption
- Save money
- Heated Point-of-Use systems
- Complete heated coverage on demand
- No wasted, unheated water to drain
This system includes Enhanced Temperature Controls that enable the customer to control the recovery and response time for their processes. This enhancement reduces temperature drops and spikes when alternating between demand and recirculation modes. This allows customers to take control of their processes and not be limited by system set parameters. Processes have different requirements, and this flexibility ensures that the heating system works best for each process.
The DI Aquarius-ECO™ system includes Power-to-Flow™, an innovative algorithm designed to provide accurate temperature even when flow, temperature, and voltage fluctuate. This proven technology measures incoming flow and temperature at various stages in the heating process, and then it adjusts the power applied to each heating zone based on those measurements. This allows the system to:
- React quickly to flow variations
- Provide accurate output temperature
- Reduce excessive temperature drops and overshoots
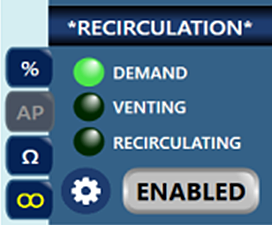
Controls: User-friendly GUI enables users to easily change between single pass-demand and recirculation modes.
The DI Aquarius® heating system has utilized this algorithm for more than 10 years within hundreds of units in some of the largest Fabs worldwide. We have also worked on variations of the system to improve response times and provide more accurate heating to meet our customer’s demanding specifications. The Aquarius-ECO™ is the premier DI water heating solution built on top of that robust platform.
Contact us today to learn how the proven Aquarius-ECO™ water-conservation heating system can save your water, cut your costs, or improve your processes.
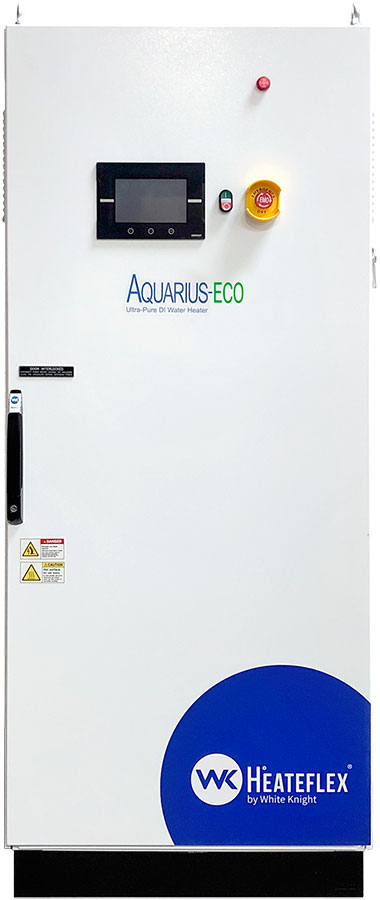
Aquarius-ECO™ Delivery & Recirculation Modes
The Aquarius-ECO™ Recirculation Mode saves process time and reduces water usage by negating trickle flow and keeping ultra-pure water in your system heated and ready for use. While in Recirculation Mode, no fluid is being used at the process and fluid is being diverted back to the heating system. The heating system engages in energy conservation, while maintaining temperature control while in the recirculation mode. Demand mode allows the user to send fluid to their process when it is in demand. Venting is used when recirculation mode is prepared to initiate, and bubbles need to be removed from the plumbing and pump.
Demand Mode: Demand mode allows the user to send fluid to their process when it is in demand. Venting is used when recirculation mode is prepared to initiate, and bubbles need to be removed from the plumbing and pump.
Recirculation Mode: The Aquarius-ECO™ Recirculation Mode saves process time and reduces water usage by negating trickle flow and keeping ultra-pure water in your system heated and ready for use. While in Recirculation Mode, no fluid is being used at the process and fluid is being diverted back to the heating system. The heating system engages in energy conservation, while maintaining temperature control while in the recirculation mode.
Aquarius-ECO™ Performance
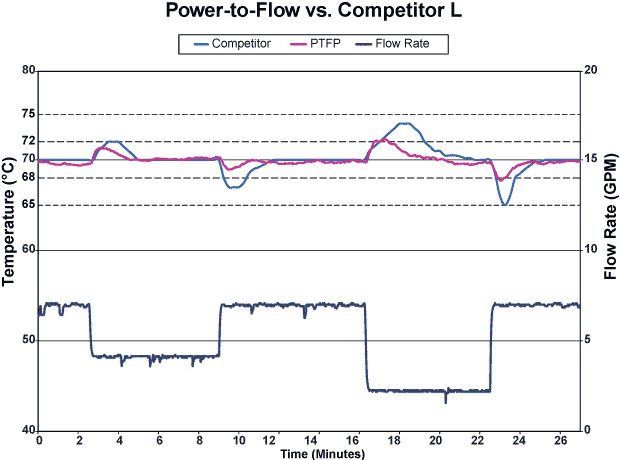
Ultrapure Water Applications
Heated Ultrapure Water (UPW) is critical in Semiconductor fabrication. The industry has stringent requirements for cleanliness, precision, and reliability because miniscule impurities can cause significant defects at the nanometer-scale of modern semiconductor components. Maintaining an environment with ultra-pure water is crucial for achieving high yields, consistent device performance, and overall quality in the most stringent semiconductor manufacturing processes. Below are some of the key processes that rely on ultra-pure water.
Chemical and Particle Contamination Control: Semiconductor fabrication involves processes that are extremely sensitive to contaminants, both in terms of chemicals and particles. Even trace amounts of impurities can lead to defects in the final product. Ultrapure water helps minimize the introduction of contaminants that could compromise the quality and performance of the devices.
Etching and Cleaning Processes: Etching is a process used to remove specific layers of material from a semiconductor wafer to create intricate patterns. Additionally, cleaning steps are crucial to remove residues and contaminants from the wafer surface between various manufacturing steps. Ultrapure water is used in these processes to ensure that no unintended reactions or contamination occur.
Photolithography: Photolithography is a central process in semiconductor manufacturing where patterns are projected onto a wafer to define the locations of various components. A layer of photoresist is applied to the wafer surface before exposure to light. Clean and ultra-pure water is used to rinse away excess photoresist and other contaminants after the exposure, ensuring accurate pattern transfer.
Chemical Vapor Deposition (CVD) and Atomic Layer Deposition (ALD): These processes are used to deposit thin films of materials onto the wafer’s surface to build up the complex structures of modern semiconductor devices. Ultrapure water is used in between deposition steps to remove any residue or particles that could affect the quality of the deposited films.
Ion Implantation: In this process, ions are implanted into the semiconductor substrate to alter its electrical properties. Ultrapure water is used for cleaning the wafer surface after ion implantation to remove any residual particles or chemicals.
Dilution and Mixing: Many chemicals used in semiconductor manufacturing need to be mixed or diluted to precise concentrations. Ultrapure water serves as the base for these mixtures, ensuring accuracy in chemical compositions.
Preventing Corrosion and Scaling: Ultrapure water helps prevent the buildup of mineral deposits and scale in the complex equipment used in semiconductor manufacturing. These deposits could negatively impact the performance and reliability of the equipment..
Metrology and Inspection: Ultrapure water is also used in metrology and inspection tools to ensure accurate measurements and imaging of semiconductor structures. Cleanliness is critical for obtaining precise data.
Importance of Water Conservation
Water conservation is of great importance to semiconductor manufacturers. Given the global focus on sustainable practices and environmental stewardship, semiconductor manufacturers are increasingly recognizing the need to adopt water conservation measures as an integral part of their operations. These measures benefit the industry’s long-term viability, and they contribute to a more environmentally responsible and resource-efficient future.
Sustainability: As the demand for semiconductors and electronic devices continues to grow, the semiconductor industry’s water usage has also increased. This places a strain on local water resources, especially in regions where water scarcity is a concern. By practicing water conservation, semiconductor manufacturers can contribute to sustainable water management and help ensure a stable water supply for their operations and local communities.
Environmental Impacts: The semiconductor manufacturing process can involve a significant amount of water consumption. Water conservation efforts help reduce the environmental impact of semiconductor fabrication, including the potential pollution of water bodies due to the release of wastewater containing chemicals and contaminants used in the manufacturing process.
Cost Savings: Water is a valuable resource, and its availability and cost can vary based on location and regional factors. Implementing water conservation measures can lead to substantial cost savings for semiconductor manufacturers by reducing water consumption, wastewater treatment costs, and associated utility bills.
Regulatory Compliance: Many regions have strict regulations and permits in place to control water usage and the discharge of industrial wastewater. By conserving water, semiconductor manufacturers can ensure compliance with these regulations and avoid potential fines or legal issues.
Corporate Social Responsibility: Companies in the semiconductor industry are increasingly expected to demonstrate their commitment to environmental sustainability and responsible resource management. Water conservation practices enhance a company’s reputation and align with corporate social responsibility goals, which can attract environmentally conscious customers and investors.
Water-Intensive Processes: The semiconductor manufacturing process involves various water-intensive steps, including cleaning, rinsing, and cooling. Finding ways to optimize these processes and minimize water usage can have a significant impact on overall consumption.
Innovation and Efficiency: The push for water conservation encourages semiconductor manufacturers to innovate and adopt more efficient manufacturing processes. This drive for efficiency can lead to technological advancements that not only conserve water but also improve overall process performance and product quality.
Water Reuse and Recycling: Water conservation efforts often involve exploring options for water reuse and recycling within the manufacturing process. Treating and reusing water for certain non-critical processes can significantly reduce overall water demand.
Supply Chain Considerations: Water scarcity can impact the entire supply chain of semiconductor manufacturing, affecting the availability and cost of critical materials. By prioritizing water conservation, manufacturers can help secure their supply chains against potential disruptions caused by water shortages.