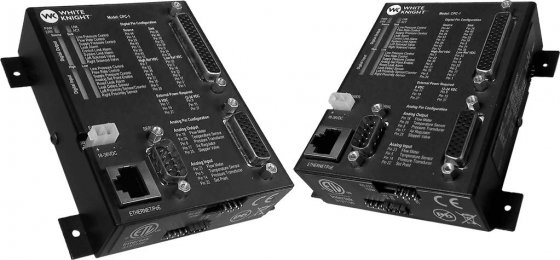
Overview
The programmable closed-loop controller (CPC-1) automatically maintains system fluid pressure or flow rate in high-purity chemical processes and delivery systems. It monitors and controls pneumatic pumps and pump accessories to provide complete closed-loop systems.
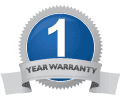
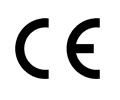
Features & Benefits
The CPC-1 monitors and controls pneumatic pump systems. It supports pressure control and flow control operation modes to manage the system using feedback from a pressure transducer (no delay) or a flow meter (two second signal delay), respectively. It also supports supply pressure control operation to manage the system without feedback control.
- Automatically maintains system pressure or flow rate
- Simple Plug-&-Play integration using standard protocols
- Flow stability in pressure transitions that is independent of filter loading, viscosity, or temperature
- Adjustable flow rate or pressure set point
- Maintains line pressure in dead-head without continued cycling of the pump
- Maintains delivery pressure as demand and line restrictions change
- High temperature capability
- Software interface simplifies setup
- Real-time feedback for flow rate, supply pressure, line pressure, and temperature
- Quickly switch between control modes
- Customizable alarms for control limit, system limit, maintenance, and leak detection
- Input and output communication through analog and digital signals
- Compatible with shuttle-, fiber optic-, and proximity-driven bellows pumps
- Supports parallel operation with multiple White Knight pumps
System Setups
The CPC-1 sends an analog signal to an electro-pnuematic proportional regulator. The regulator applies pressure to the pump. The pump pressurizes the fluid line causing flow. Sensors placed in the fluid line send analog signals to the CPC-1 to maintain the process. Simultaneously, the CPC-1 communicates to external alarms, PLC, or Windows-based computer, which allows the CPC-1 to integrate into various tool designs.
Communications
Setup controller using a Windows computer via a standard RS-232 communication protocol or a 10/100 Base-T Ethernet port. It supports automatic IP Address assignment over DHCP Network.
Power Requirements
- CPC-1 power consumption 2.5 watts typical with maximum of 4 watts.
- High-power sourcing outputs (12 –24 VDC, 500 mA)
- Low-power outputs (5 –24 VDC, 25 mA)
Wiring Connections
Digital I/O Connections: 44 Pin HD D-Sub Connector
Digital Inputs Include:
- Turn on pressure control
- Turn on flow control
- Turn on set supply air
- Turn on set point change via Analog input
- Leak sensor input
- Reset leak sensor alarm
- Proximity sensor input left
- Proximity sensor input right
Digital Outputs Include:
- Pressure control on
- Flow control on
- Supply air on
- Alarm: Leak detected
- Alarm: Out of control limits
- Alarm: Near System Capacity
- Solenoid: Left signal
- Solenoid: Right signal
* Digital inputs are configurable to voltage reference high or low.
* Digital outputs are configurable to be voltage source or sink.
* Digital ports must be powered with an external source.
Analog I/O Connections: 26 Pin HD D-Sub Connector
Analog Inputs Include:
- Flow meter signal
- Pressure transducer signal
- Temperature sensor
- Desired set point
Analog Outputs Include:
- Flow meter signal
- Pressure transducer signal
- Temperature signal
- Air regulator signal
* Analog inputs can be configured to be 0-5 VDC, 0-10 VDC, or 4-20 mA.
* 4-20 mA output requires the optional White Knight signal converter.
Dimensions
Configuration
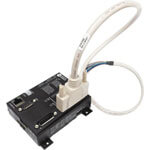
Digital I/O cable to wire leads
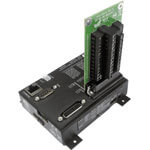
Breakout board to screw terminals
High-Purity Closed-Loop Pump Systems
Automatically maintain laminar flow or steady pressure. White Knight closed-loop systems feature metal-free PTFE pumps. They provide stable temperatures, dead-head, and suction lift.
Control your high-purity chemical processes and delivery systems. Simplify process automation to save time, resources and reduce costs.
- ≤ 140 lpm (36 gpm) flow rates
- ≤ 7 Bar (100 psi) pressures
- ≤ 210°C (410°F) temperatures
- Maintain stable temperatures
- No metals, no corrosion
- No elastomer O-rings, no leaks
- No electric motors, no heat rise
- No impellers, no microbubbles