Overview
White Knight debubblers reduce bubbles from high-purity chemical delivery and wafer process systems. They redirect flow to the surface so that bubbles rise out of the fluid. They feature 4-in inside diameters for greater debubbling surface area. All White Knight debubblers utilize leak-free tongue-and-groove seals and offer liquid level sensor options.
Features & Benefits
- Process-safe, chemically-resistant PTFE and PFA flow paths
- Up to 7 Bar (100 psi) for high flow rates for faster processes
- Up to 100°C or 210°C fluid temperatures
- Leak-Free Tongue-and-Groove seals
- Easy setup and maintenance without welding
- Ideal for chemical delivery and wafer process debubbling
More Information:
CBA Series Debubblers
CBA Series debubblers are available in various connectable pipe lengths with models capable of up 1-6 liter volumes. They offer additional mounting and liquid level sensor options.
- Up to 100°C (212°F) fluid temperatures
- Leak-Free Tongue-and-Groove seals
- Models capable of up 1-6 liter volumes
- Liquid level sensor and mounting options
CBU Series Debubblers
CBU Series debubblers capable of up to 210°C (410°F) fluid temperatures. They feature Synchro-Thread™, tongue-and-groove seals, and dual-static crush seals to ensure safe, reliable operation at high-temperatures.
- Synchro-Thread™ for fluids up to 210°C (410°F)
- Leak-Free Tongue-and-Groove seals and reliable dual-static crush O-ring seals
- Capable of 1-liter volume
- Liquid level sight tube options
Operation
White Knight debubblers redirect flow upward and slows the fluid so that air bubbles rise within the chamber. As air collects at the top, the liquid level drops until the lower sensor detects a low liquid level and signals a valve to open to releases air via the drain vent. As air vents, the liquid level rises until the upper sensor detects a high liquid level and signals the valve to close.
Comparison
Debubbler Models | ||
---|---|---|
PTFE, PFA flow paths |
||
Maximum Temperature |
100°C (212°F) |
210°C (410°F) |
Maximum Pressure |
7 Bar (100 psi) |
7 Bar (100 psi) |
Maximum Volume |
1-6 L |
1 L |
Tongue-and-Groove Seals |
||
Dual-Static Crush Seals |
||
Synchro-Thread™ |
||
Mounting Bracket Options |
1-3 brackets or base mount |
Base mount |
Sensor Options |
1-3 sensors on body or brackets |
Sensors on liquid level sight tube |
Warranty |
2 Year |
2 Year |
Temperature Curves
CBA Temperature Curves
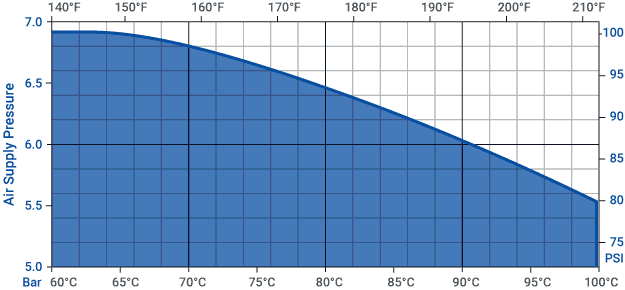
CBA Temperature Curves
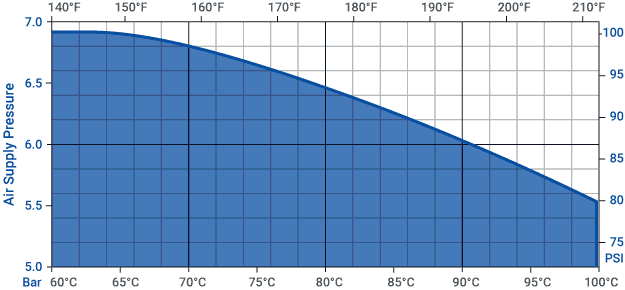
CBU Temperature Curves
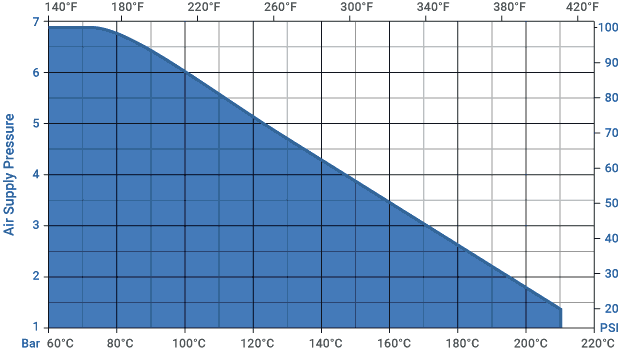
Debubbler Applications
Remove Bubbles After Pumps
Chemical enters the debubbler through the stand tube. Level sensors 1 and 2 control the collected air volume in the debubbler. Collected air exits through the vent line.
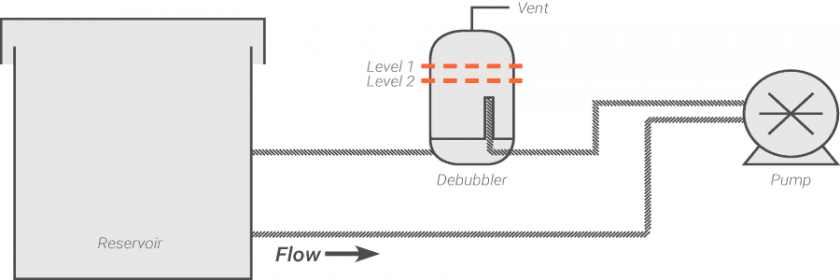
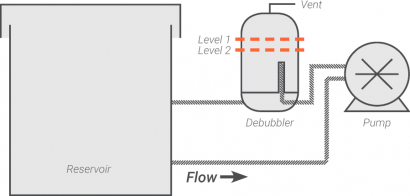
Remove Bubbles Before Pumps
Chemical is pulled into the debubbler through the stand tube. Level sensors 1 and 2 control air collection level to purge the collected air, a vacuum is required to remove collected air. This can be achieved using a venturi-type vacuum.
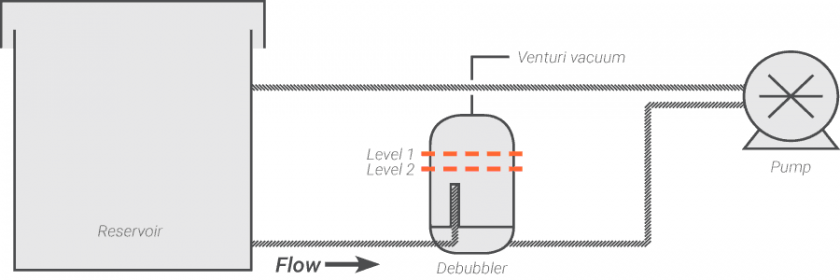
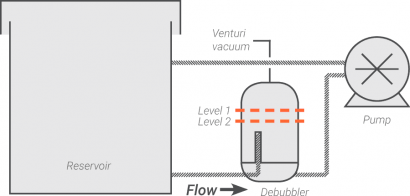
Automate Drum Change
Level sensors 1 and 2 act to keep bubbles from the drums from continuing through to the pump. Level 3 indicates an empty drum. This can be used as an automatic drum switch or as a drum empty signal.
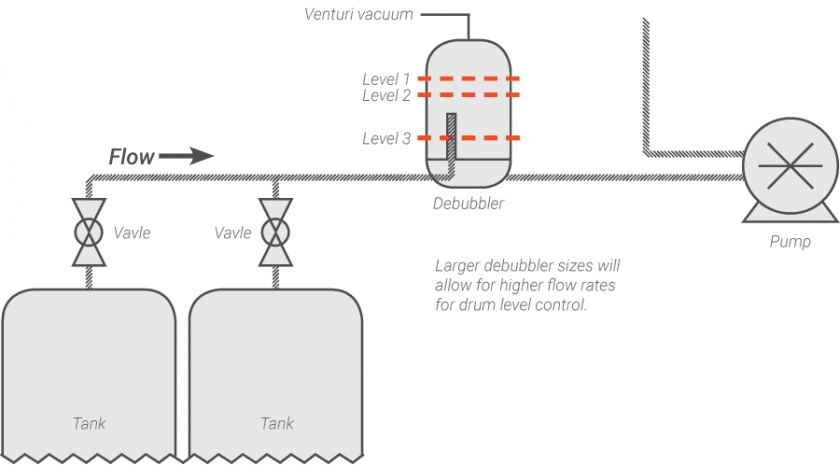
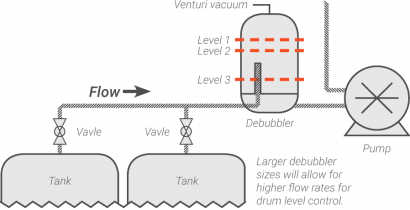
Dimensions
[mm] inches
CBA Dimensions
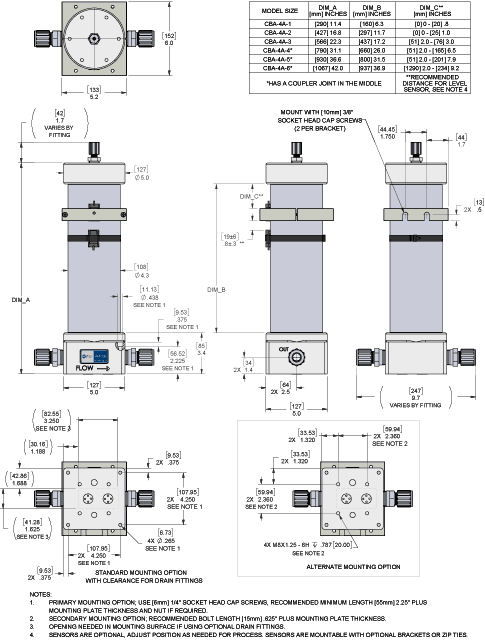
mm (in) | A | B |
---|---|---|
1 liter | 295 (11.6) | 132 (5.2) |
2 liter | 434 (17.1) | 272 (10.7) |
3 liter | 572 (22.5) | 409 (16.1) |
4 liter | 798 (31.4) | 632 (24.9) |
5 liter | 935 (36.8) | 772 (30.4) |
6 liter | 1074 (42.3) | 980 (38.6) |
CBU Dimensions
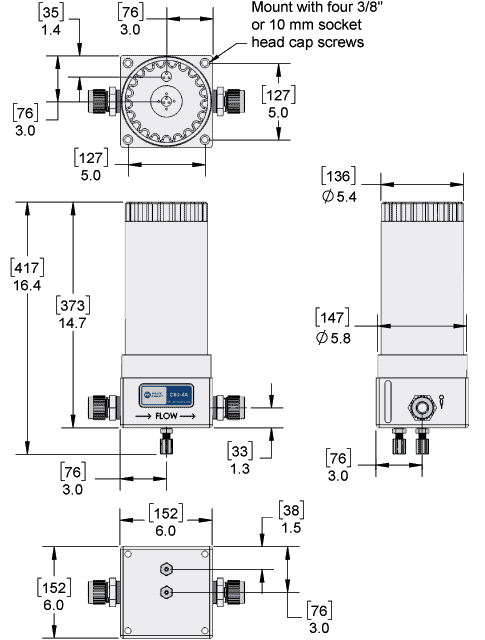